Wir befinden uns in einem Zeitalter, in welchem technologische Fortschritte das Tempo der Innovationen unermüdlich antreiben. Im Zuge dessen nimmt die Digitalisierung im Maschinenbau eine Schlüsselrolle ein, die nicht nur die zukunft der industrie repräsentiert, sondern sie aktiv gestaltet. Der Trend zur digitalen Transformation ist längst kein Novum mehr; er verkörpert die unaufhaltsame Evolution hin zu Industrie 4.0.
In diesem Wandel erkennen wir, dass Maschinenbauunternehmen im Jahr 2023 nicht lediglich Zuschauer bleiben dürfen, sondern vielmehr Beteiligte und Gestalter des technologischen Fortschritts werden müssen, um innovativ und wettbewerbsfähig zu bleiben.
Schlüsselerkenntnisse zur Digitalisierung im Maschinenbau
- Die Digitalisierung stellt den Grundstein für zukünftige Wettbewerbsfähigkeit und Nachhaltigkeit in der Maschinenbaubranche dar.
- Maschinenbauunternehmen müssen sich den Herausforderungen der Industrie 4.0 stellen, um ihre Marktposition zu stärken.
- Technologische Innovationen wie IoT und künstliche Intelligenz sind treibende Kräfte der digitalen Transformation.
- Digitale Prozesse eröffnen neue Möglichkeiten für Effizienzsteigerung und innovative Geschäftsmodelle.
- Die Vernetzung von Produktionssystemen verbessert die betrieblichen Abläufe und stärkt die Kollaboration entlang der Lieferkette.
- Die Anpassungsfähigkeit und kontinuierliche Weiterbildung der Fachkräfte sind entscheidend für den Erfolg der digitalen Transformation.
Maschinenbau im Zeitalter der Digitalisierung
Die Welt des Maschinenbaus hat einen Punkt erreicht, an dem das Thema Digitalisierung nicht länger ein Randphänomen, sondern ein zentraler Bestandteil der Branche oder des Branchenbildes ist. Mit der Digitalisierung werden Maschinen und Anlagen smarter, die Produktion effizienter und der gesamte Sektor zukunftsorientierter. Dieser Innovationsgeist, angetrieben durch Industrie 4.0, eröffnet neue Horizonte für Unternehmen, die bereit sind, sich anzupassen und die Möglichkeiten der Technologie voll auszuschöpfen.
Die Geschichte des Maschinenbaus ist geprägt von kontinuierlichen Veränderungen und technologischen Sprüngen. Doch die aktuelle Welle der digitalen Transformation stellt eine der grundsätzlichsten Herausforderungen dar, mit der sich Unternehmen konfrontiert sehen. Sie sind gezwungen, traditionelle Produktionsverfahren zu überdenken und neuartige Konzepte zu adaptieren, um sich in der vernetzten Welt der Industrie 4.0 im Maschinenbau zu behaupten.
Die digitale Revolution im Maschinenbau ist nicht nur eine Frage der Technologie, sondern auch der Mentalität.
Wir beobachten, wie sich führende Unternehmen bereits jetzt proaktiv verhalten, um die Chancen, die sich aus der Digitalisierung ergeben, zu nutzen. Sie investieren in intelligente Fertigungssysteme, nutzen datengetriebene Analysen für präzisere Prozesse und entwickeln Geschäftsmodelle, die auf die Bedürfnisse des digitalen Zeitalters zugeschnitten sind. Die wichtigsten Punkte dabei sind:
- Erkennen der Notwendigkeit einer digitalen Erneuerung
- Investitionen in moderne Technologien und Fachwissen
- Entwicklung neuer, digital orientierter Geschäftsbereiche
- Transformation hin zu agilen und vernetzten Betriebsstrukturen
Entwicklungsphase | Traditioneller Maschinenbau | Digitaler Maschinenbau |
---|---|---|
Produktionsverfahren | Manuelle und mechanisierte Fertigung | Automatisierte und vernetzte Fertigung |
Innovationstempo | Langsame Iterationen | Schnelle, iterative Entwicklungszyklen |
Wettbewerbsstrategie | Kostenorientierung | Kunden- und serviceorientiert |
Datennutzung | Begrenzt und isoliert | Umfassend und integriert |
Dieser Transformationsprozess verändert nicht nur einzelne Facetten, sondern gestaltet die gesamte Ausrichtung der Betriebe im Maschinenbau neu. Der Schlüssel zum Erfolg liegt in der Bereitschaft, bestehende Strukturen aufzubrechen und innovative Denkmuster zu fördern. Der Maschinenbau wird im Laufe der digitalen Transformation zu einem Vorreiter der modernen Industrie und trägt maßgeblich zur Definition der Industrie 4.0 im Maschinenbau bei.
Grundlagen der Digitalisierung im Maschinenbau
Die Digitalisierung betrifft alle Ebenen des Maschinenbaus und bildet die Grundlage für eine nachhaltig erfolgreiche Zukunft der Branche. Dabei geht es nicht nur um die Implementierung neuer Technologien, sondern auch um eine tiefgreifende Veränderung der betrieblichen Abläufe und Geschäftsmodelle.

Der Maschinenbau bietet dabei ein einzigartiges Potenzial für Digitalisierungsstrategien, da er aufgrund seiner technischen Komplexität und Innovationskraft enorme Synergieeffekte mit digitalen Technologien erzielen kann.
Wir erleben, wie Grundlagen der Digitalisierung nicht nur theoretische Konzepte bleiben, sondern in praxisorientierte Lösungen umgesetzt werden. Diese Entwicklung haben wir es uns zur Aufgabe gemacht, näher zu beleuchten und deren Einfluss auf die Wertschöpfungsketten im Maschinenbau zu untersuchen.
Die Digitalisierung im Maschinenbau ist die essenzielle Voraussetzung, um in der modernen Industriewelt konkurrenzfähig zu bleiben und die Produktivität zu steigern.
Im Folgenden betrachten wir einige der fundamentale Veränderungen, die bei der Transformation betrieblicher Prozesse durch die Digitalisierung essentiell sind:
- Konnektivität und Datenintegration über alle Produktionsbereiche hinweg
- Automatisierung von Fertigungsprozessen und Einführung von intelligenten Systemen
- Steigerung der Prozesseffizienz durch Analyse großer Datenmengen
- Entwicklung neuer Geschäftsmodelle, die auf Datennutzung und -analyse basieren
- Anwendung von Predictive Maintenance zur vorausschauenden Wartung und Fehlervermeidung
Bereich | Traditionelle Vorgehensweise | Digitale Neuausrichtung |
---|---|---|
Produktionsketten | Isolierte Einheiten | Integriert und digital vernetzt |
Datennutzung | Beschränkt auf Einzelprozesse | Umfassend, zur Optimierung des gesamten Betriebs |
Wartungsstrategien | Reaktiv | Proaktiv durch Predictive Analytics |
Entwicklung neuer Produkte | Langwierig und ressourcenintensiv | Agil und kundenorientiert durch Digital Engineering |
Qualitätssicherung | Endkontrollen | Kontinuierlich und prozessbegleitend durch Echtzeit- Überwachung |
Diese tiefgreifenden Veränderungen erfordern eine kontinuierliche Weiterbildung und ein Umdenken in allen Unternehmensbereichen. Die Grundlagen der Digitalisierung im Maschinenbau sind mehr als nur eine technische Erneuerung - sie sind ein komplexer Prozess, der Bereitschaft zur Veränderung und zur Anpassung an neue, digitale Realitäten verlangt.
Chancen der Industrie 4.0 für Maschinenbauunternehmen
Die vierte industrielle Revolution, bekannt als Industrie 4.0, bietet für die meisten Maschinenbauunternehmen zahlreiche Chancen und Risiken. Einerseits stehen sie vor der Herausforderung, die neuen Technologien effizient zu integrieren und die eigene Wettbewerbsfähigkeit zu stärken.
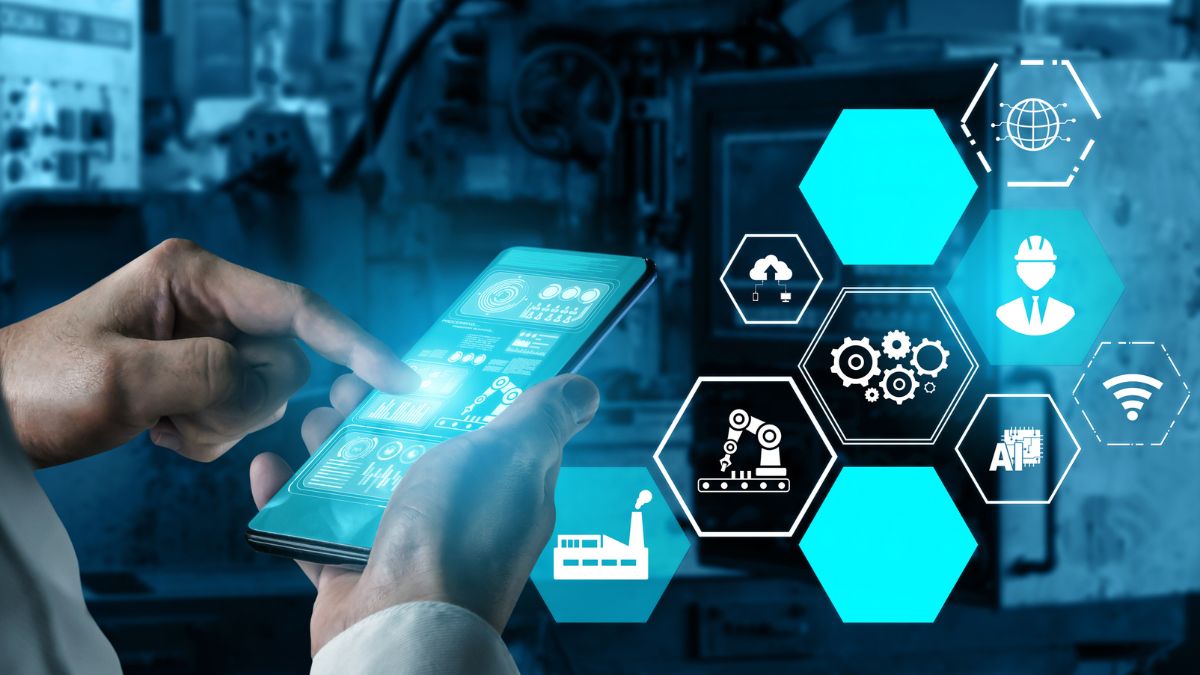
Andererseits eröffnen sich durch smarte, vernetzte Systeme ganz neue Möglichkeiten, die Effizienz zu steigern, innovative Geschäftsmodelle zu entwickeln und die Produktion zu optimieren. Unternehmen müssen sich diesem Wandel stellen, um langfristig erfolgreich zu bleiben.
Effizienzsteigerung durch digitale Prozesse
Digitale Prozesse sind das Herzstück der Industrie 4.0 und tragen entscheidend dazu bei, Abläufe im Maschinenbau effizienter und flexibler zu gestalten. Durch die Digitalisierung wird eine enorme Effizienzsteigerung ermöglicht, sei es durch intelligentes Energiemanagement, optimierte Wartungsintervalle oder eine gesteigerte Maschinenleistung. Die folgende Tabelle zeigt exemplarisch, wie Unternehmen von digitalen Prozessen profitieren können:
Digitaler Prozess | Vorteil |
---|---|
Integrierte Sensorik in Maschinen | Ermöglichung einer vorausschauenden Wartung und Ausfallprävention |
Automatisierte Produktionssteuerung | Steigerung der Produktivität und schnelle Reaktion auf Marktanforderungen |
Digitale Qualitätsüberwachung | Verbesserung der Produktqualität und Reduzierung der Fehlerquote |
Echtzeit-Datenanalyse | Effiziente Ressourcenplanung und -verteilung |
Innovative Geschäftsmodelle und Services
Mit dem Einzug digitaler Technologien im Maschinenbau entstehen auch ganz neue Geschäftsmodelle. Diese basieren auf der Auswertung von Daten, dem Anbieten von digitalen Services und einer starken Kundenorientierung. Ein Beispiel hierfür ist das "Pay-per-Use"-Modell, bei dem Kunden nicht mehr für die Maschine an sich zahlen, sondern für deren Nutzung. Solche adaptiven Modelle erhöhen die Attraktivität für die Kunden und schaffen gleichzeitig neue Umsatzströme für das Unternehmen.
Digitale Services und Geschäftsmodelle sind die Basis für eine Zukunft, in der Flexibilität und innovative Lösungen das Überleben am Markt sichern.
Vernetzte Produktionssysteme und deren Vorteile
Die Vernetzung von Produktionssystemen ist ein weiterer entscheidender Aspekt der Industrie 4.0. Durch intelligente, vernetzte Systeme können einzelne Produktionsmodule effizient miteinander kommunizieren und selbstständig Optimierungen vornehmen. Dies führt zu einer optimierten Fertigung, geringeren Produktionskosten und einer höheren Anpassungsfähigkeit an kundenspezifische Anforderungen.

Zusammenfassend lässt sich sagen, dass die Chancen der Industrie 4.0 für Maschinenbauunternehmen vielfältig sind. Um diese zu nutzen, müssen Unternehmen sich der digitale Transformation öffnen, innovative Lösungen umsetzen und ihre Systeme vernetzt und smart gestalten. Denn nur so können sie ihre Wettbewerbsfähigkeit in einem sich schnell verändernden Marktumfeld behaupten und ausbauen.
Herausforderungen für den Maschinenbau bei der Digitalisierung
Der digitale Wandel bringt für Maschinenbauer grundlegende Umstrukturierungen mit sich, denen sich Maschinenbauunternehmen stellen müssen, um zukunftsfähig zu bleiben. Dieser Wandel stellt kontinuierlich hohe Anforderungen an Firmen, die umfassende Ressourcen in finanzieller, personeller und strategischer Hinsicht erfordern. Im Folgenden werden zentrale Herausforderungen für den Maschinenbau erörtert, die für eine erfolgreiche Digitalisierung überwunden werden müssen.
- Fachkräftemangel: Eine der drängendsten Herausforderungen ist der Mangel an qualifizierten Fachkräften, die sowohl über ingenieurwissenschaftliches Know-how als auch über digitale Kompetenzen verfügen. Der Bedarf an Weiterbildung und die Rekrutierung von Talenten mit entsprechendem technologischen Wissen sind zentrale Bausteine, um diesen Mangel zu beheben.
- Finanzielle Investitionen: Für die Implementierung digitaler Technologien sind Anfangsinvestitionen unausweichlich. Hierbei müssen Unternehmen Kosten-Nutzen-Abwägungen treffen und langfristig in digitale Infrastrukturen investieren. Die Finanzierung von Innovationsprojekten bleibt eine große Hürde, insbesondere für kleinere und mittelständische Unternehmen.
- Widerstände gegenüber Veränderungen: Nicht selten stoßen Digitalisierungsvorhaben auf interne Widerstände. Die Angst vor Veränderung und dem Verlust des Gewohnten erschwert die Umsetzung neuer Geschäftsprozesse. Kontinuierliche Kommunikation und das Einbeziehen aller Mitarbeiter in den Transformationsprozess sind essentiell, um diesem entgegenzuwirken.
Um den technologischen Fortschritt effektiv zu nutzen, müssen Unternehmen des Maschinenbaus den digitalen Wandel als Chance begreifen und aktiv Herausforderungen angehen.
Dies bedeutet das folgende Punkte in der Bewertung unumgänglich sein werden:
- Strategische Neuausrichtung auf digitale Geschäftsmodelle
- Adaption neuer Technologien und Methoden
- Schaffung einer offenen Unternehmenskultur gegenüber Digitalisierung
- Kooperationen mit technologischen Partnern und Start-ups
Herausforderung | Konsequenzen | Notwendige Maßnahmen |
---|---|---|
Fachkräftemangel | Eingeschränkte Umsetzungsfähigkeit digitaler Innovationen | Weiterbildungsprogramme, Förderung von Talenten |
Finanzielle Investitionen | Verzögerte Modernisierung | Strategische Finanzplanung, Fördermittel |
Interne Widerstände | Geringe Innovationsgeschwindigkeit | Change Management, Partizipative Prozesse |
Die Digitalisierung stellt unweigerlich Herausforderungen für den Maschinenbau dar, die jedoch gleichzeitig als Katalysator für Wachstum und Innovation wirken können. Es ist unabdingbar, dass Unternehmen kontinuierlich ihre Strukturen hinterfragen und flexibel auf die Anforderungen des digitalen Wandels reagieren, um langfristig am Markt bestehen und wachsen zu können.
Technologische Treiber der Digitalisierung
Die fortschreitende Digitalisierung im Maschinenbau wird durch eine Reihe technologischer Innovationen angetrieben, die traditionelle Produktionsparadigmen vollständig transformieren. Zu diesen Innovationstreibern zählen insbesondere die künstliche Intelligenz (KI), Machine Learning, Big Data Analytics sowie cloud-basierte Technologien.

Diese Elemente agieren nicht isoliert, sondern bilden in ihrer Gesamtheit die Grundlage für eine umfassende Automatisierung und intelligente Fertigungsumgebungen, die die Effizienz und Produktivität von Maschinenbauunternehmen erheblich steigern.
Künstliche Intelligenz und Machine Learning im Einsatz
Wir erleben, wie die KI-Technologie und Machine Learning die Art und Weise, wie Maschinenbauunternehmen ihre Abläufe gestalten, grundlegend verändert. Durch die Einführung dieser Technologien werden Maschinen in der Lage sein, selbsttätig zu lernen und Optimierungsaufgaben zu übernehmen. Dies eröffnet ein neues Spektrum an Möglichkeiten, von der Produktentwicklung bis zur Qualitätssicherung, während gleichzeitig die Effizienz gesteigert und Ressourcen geschont werden.
Die Intelligenz von morgen im Maschinenbau basiert auf der künstlichen Intelligenz und dem Machine Learning von heute.
Big Data Analytics für maschinengenerierte Daten
Die Anwendung von Big Data Analytics spielt eine zentrale Rolle in der Wertschöpfungskette, indem sie es ermöglicht, aus der Flut an Daten, die im Produktionsprozess generiert werden, wertvolle Erkenntnisse zu ziehen.
Die Sammlung, Speicherung und Analyse dieser enormen Datenmengen, oft bezeichnet als "Maschinendaten", ermöglicht es den Maschinenbauunternehmen, ihre Prozesse präziser zu steuern, Ausfallzeiten zu minimieren und letztlich die Produktqualität zu maximieren.

Big Data Analytics transformiert Rohdaten in wertvolles Wissen, das für Innovationen und langfristigen Geschäftserfolg entscheidend ist.
- Effektive Vorhersage von Wartungsbedarf durch Datenanalyse
- Optimierte Prozesssteuerung und Automatisierung durch präzise Echtzeit-Daten
- Beschleunigung von Forschung und Entwicklung durch maschinelles Lernen
Die anschließende Tabelle veranschaulicht die Bandbreite der Anwendungsgebiete für KI und Big Data Analytics in Unternehmen des Maschinenbaus:
Technologie | Einsatzbereich | Vorteil |
---|---|---|
KI-gesteuerte Automatisierung | Produktionslinien | Erhöhung der Betriebseffizienz und Kostenreduktion |
Machine Learning | Qualitätskontrolle | Verbesserung der Produktqualität durch prädikative Fehleranalyse |
Big Data Analytics | Prozessoptimierung | Prozessbeschleunigung und Entscheidungsfindung auf Grundlage detaillierter Daten |
In der Kombination dieser Technologien manifestiert sich die digitale Kompetenz eines modernen Maschinenbauunternehmens, welches die Innovationen der Cloud-Technologie und fortschrittliche Datenverarbeitung nutzt, um marktführend zu agieren.
Entscheidend für den Erfolg sind das Verstehen und die richtige Anwendung dieser Technologien, um die Komplexität der Daten zu meistern und in wertvolle Geschäftsintelligenz umzuwandeln. Der Erfolg des Maschinenbaus im 21. Jahrhundert wird dadurch nicht nur von mechanischer Präzision abhängen, sondern ebenso stark von der Handhabung und Implementierung fortschrittlicher digitaler Technologien.
Digitale Schnittstellen und Integration in der Fertigung
Im Kontext der Industrie 4.0 sind digitale Schnittstellen das Fundament für eine effiziente Integration verschiedenster Systeme innerhalb der smarten Fabrikationsumgebungen. Unsere fortwährende Analyse hat gezeigt, dass solide Schnittstellen zwischen Maschinen, Softwarelösungen und Produktionseinheiten entscheidend für die Umsetzung einer Automatisierung und Optimierung in der Fertigung sind.
Ohne diese Kernelemente wäre eine smarte Fabrik, im Sinne einer Smart Factory, kaum realisierbar.

Mit dem Ziel, die Produktionsprozesse zu verschlanken, Ausfallzeiten zu minimieren und eine reibungslose Kommunikation zwischen den einzelnen Fertigungselementen sicherzustellen, tragen digitale Schnittstellen maßgeblich zur Automatisierung und Effizienz in Produktionsbetrieben bei.
Sie ermöglichen es einem System, Informationen zu sammeln, zu analysieren und daraufhin Entscheidungen zu treffen, die die Performance und Qualität der Produktion erhöhen.
Digitale Schnittstellen verwandeln eine herkömmliche Produktionsstätte in eine innovative Smart Factory, in der nahtlose Integration und Kommunikation möglich sind.
Natürlich ist die Implementierung solcher Schnittstellen mit Herausforderungen verbunden. Es müssen kompatible Standards gesetzt und Datenschutz gewährleistet werden, um die Sicherheit und Effizienz dieser technologischen Investitionen zu garantieren. Das bedeutet:
- Entwicklung einheitlicher Kommunikationsprotokolle
- Gewährleistung von Datensicherheit und Schutz
- Flexible Integration neuer Technologien und Systeme
- Synchronisation und Echtzeitüberwachung aller Abläufe
Vorteil digitaler Schnittstellen | Einsatzbereich | Ergebnis |
---|---|---|
Erhöhte Transparenz | Anlagenüberwachung | Kontinuierliche Leistungsoptimierung |
Beschleunigte Produktionsprozesse | Auftragsabwicklung | Gesteigerte Effizienz bei der Lieferkette |
Prozessübergreifende Vernetzung | Qualitätssicherung | Frühzeitige Fehlererkennung und -behebung |
Automatisierte Anpassungen | Wartung und Instandhaltung | Reduktion von Stillstandszeiten |
Im Ergebnis bilden die digitale Schnittstellen und ihre Integration in der Fertigung eine wesentliche Säule auf dem Weg zur Realisierung einer Smart Factory. Sie stellen nicht nur die Grundlage für Automatisierung und Effizienz dar, sondern sind auch der Schlüssel zur langfristigen Wettbewerbsfähigkeit und Innovation im Maschinenbausektor.
Auswirkungen der Digitalisierung auf das Engineering
Wir erkennen, dass die Auswirkungen der Digitalisierung auf das Engineering weitreichend sind und Chancen für die Branche darstellen. Der Übergang zu digital Engineering ermöglicht dabei innovative Lösungen, die komplexe Probleme effizienter lösen und die Entwicklungszeiten verkürzen.
Anforderungen an die Qualifikation von Fachkräften
Die Digitalisierung im Ingenieurwesen resultiert in veränderten Anforderungen an die Qualifikation von Fachkräften. Dies bedingt eine Notwendigkeit für anhaltende Weiterbildung und Umschulung, mit einem speziellen Fokus auf digitale Kompetenzen. Ein Fachkräftemangel in diesem Bereich könnte die Fortschritte im Engineering maßgeblich behindern.
Die Qualitätssicherung im Engineering-Prozess hat sich durch digitale Technologien grundlegend gewandelt und fordert neue Qualifikationsprofile.
Folgende digitale Kompetenzen müssen zukünftig entwickelt werden:
- Erweiterung des Kompetenzspektrums in Richtung digitaler Tools und Software
- Zielgerichtete Schulungen zur Bedienung von hochmoderner Engineering-Software
- Absicherung der Zukunftsfähigkeit durch lebenslanges Lernen und Anpassungsbereitschaft
Auswirkung | Bedarf an Fachkräften | Reaktion des Bildungsbereichs |
---|---|---|
Erhöhte Komplexität der Aufgaben | Spezialisierte Fachkräfte mit Programmier- und Systemkenntnissen | Anpassen von Curricula, Implementierung neuer Studiengänge |
Wandel in Entwicklungsprozessen | Agile Arbeitsmethoden verstehen und anwenden können | Trainings und Workshops zu agilen Methoden und Prozessen |
Notwendigkeit von interdisziplinärer Kompetenz | Experten mit übergreifendem technischem und digitalem Wissen | Interdisziplinäre Studiengänge und Fortbildungen |
Integration von Security- Kenntnissen | Mitarbeiter mit Verständnis für Cyber- Sicherheit und Datenschutz | Berufsbegleitende Weiterbildungen und Zertifizierungen im Bereich Sicherheit |
Um dem Fachkräftemangel zu begegnen und eine hohe Qualität der Engineering-Prozesse sicherzustellen, ist es essentiell, Bildungsangebote kontinuierlich zu erneuern und den wachsenden Marktbedarf an digitaler Expertise zu decken. Die digitale Revolution steht somit nicht nur für technologische Veränderung, sondern auch für eine Evolution in der beruflichen Bildung und Fachkräfteentwicklung.
Die Bedeutung von Cyber-Sicherheit im digitalen Maschinenbau
Im Zuge der fortschreitenden Digitalisierung im Maschinenbau rückt das Thema Cyber-Sicherheit immer stärker in den Vordergrund. Unsere Industrie steht vor der Herausforderung, nicht nur effizient und innovativ zu arbeiten, sondern auch die Sicherheit und den Datenschutz in allen digitalen Prozessen zu gewährleisten. Es gilt, sowohl betriebliche Abläufe als auch sensible Daten vor unerlaubtem Zugriff und Cyber-Angriffen zu schützen.
Die Integration von Cyber-Sicherheitsmaßnahmen ist kein Luxus, sondern eine zwingende Notwendigkeit für moderne Maschinenbauunternehmen.
Die Implementierung eines robusten Cyber-Sicherheitskonzepts ist komplex und muss sowohl technische als auch organisatorische Aspekte umfassen. Wir betrachten daher effektive Strategien und Maßnahmen, die Unternehmen schützen und gleichzeitig Wettbewerbsvorteile sichern:
- Regelmäßige Risikoanalysen und Schwachstellenbewertungen
- Entwicklung und Durchsetzung von Sicherheitsrichtlinien
- Training der Mitarbeiter im Umgang mit sensiblen Daten
- Einsatz von Verschlüsselungstechnologien zum Schutz der Daten
- Implementierung von Überwachungssystemen zur Erkennung von Anomalien
Bereich | Bedrohungen | Maßnahmen |
---|---|---|
Datensicherheit | Phishing, Malware, Datenlecks | Firewalls, Anti-Virus-Programme, DLP-Systeme |
Netzwerksicherheit | Unautorisierte Zugriffe, DDoS-Angriffe | Netzwerk-Monitoring, Zugriffskontrollen |
Physische Sicherheit | Diebstahl, Sabotage | Zugangskontrollen, Überwachungskameras |
Endgerätesicherheit | Verlust oder Diebstahl von Geräten | Mobile Device Management, Verschlüsselung |
Anwendungs-Sicherheit | Exploits, Schwachstellen in Software | Regelmäßige Updates und Patches |
Die richtige Balance zwischen fortschrittlicher Vernetzung und kompromissloser Cyber-Sicherheit zu finden, bedeutet für Maschinenbauunternehmen, eine resilientere und zukunftssichere Industrie zu gestalten. Die Investition in Cyber-Sicherheit stellt daher eine Grundvoraussetzung dar, um im internationalen Wettbewerb bestehen zu können und vertrauenswürdige Partner in der Lieferkette zu bleiben.

Zudem spielen gesetzliche Regelungen eine zunehmende Rolle für betriebliche Sicherheitskonzepte. Neben der Einhaltung der Datenschutz-Grundverordnung (DSGVO) müssen Unternehmen spezifische Branchennormen und Standards wie ISO/IEC 27001 berücksichtigen, um den betrieblichen Anforderungen in punkto Datenschutz und Cyber-Sicherheit gerecht zu werden.
Unser gemeinsames Ziel im digitalen Zeitalter muss es sein, dass sämtliche Beteiligten im Maschinenbau ein umfassendes Bewusstsein für die Bedeutung und Implementierung von Cyber-Sicherheitsmaßnahmen entwickeln, um die digitale Transformation sicher und erfolgreich zu gestalten.
Wandel der Unternehmenskultur in Richtung einer digitalen Zukunft
Die digitale Zukunft ist nicht mehr nur eine Vision, sondern wird täglich gelebte Realität in immer mehr mittelständischen Unternehmen. Der Wandel der Unternehmenskultur ist dabei ein entscheidender Faktor, der es ermöglichet, den Herausforderungen der Digitalisierung proaktiv zu begegnen und diese zum strategischen Vorteil zu nutzen.
Es ist die Aufgabe der Führungsebene, den Wandel nicht nur zu begleiten, sondern aktiv zu vorantreiben und diesen in Einklang mit den Visionen und Zielen des Unternehmens zu bringen.
Strategien für die Förderung einer innovativen Denkweise
Um eine innovative Denkweise in der Unternehmenskultur zu verankern, bedarf es einerseits klarer Visionen und Strategien, andererseits aber auch operativer Maßnahmen, die die Kreativität und Eigeninitiative der Mitarbeiter anregen:
- Entwicklung inklusiver Führungspraktiken, die Mitsprache und Feedback fördern
- Implementierung von Innovationsprogrammen und interdisziplinären Projekten
- Investition in moderne Arbeitsumgebungen, die kollaboratives Arbeiten unterstützen
- Belohnung von Risikobereitschaft und der Einführung von Fehlerspielräumen zur Förderung von Experimentierfreudigkeit
Die Unternehmenskultur eines mittelständischen Unternehmens ist das Betriebssystem, das Innovation ermöglicht.
Die Rolle der Weiterbildung und des lebenslangen Lernens
Die Digitale Revolution bringt stetigen Wandel und erfordert daher eine kontinuierliche Qualifizierung der Fachkräfte. Eine Kultur des lebenslangen Lernens ist deshalb ein Muss für zukunftsorientierte Unternehmen.
- Aufbau einer internen Akademie zur Vermittlung digitaler Kompetenzen
- Partnerschaften mit Bildungsträgern und Hochschulen
- Bereitstellung von Zeit und Ressourcen für individuelle Weiterbildungsinitiativen
- Durchführung regelmäßiger Schulungen zu neuen Technologien und Arbeitsmethoden
Bereich | Zielsetzung | Umsetzung |
---|---|---|
Unternehmenskultur | Digitalen Wandel vorantreiben | Entwicklung von Richtlinien und Praktiken, die eine innovative Denkweise unterstützen |
Personalentwicklung | Qualifizierung der Mitarbeiter | Angebote zur Weiterbildung und zum lebenslangen Lernen schaffen |
Innovation | Neue Lösungen entwickeln | Etablieren von Strukturen, die kreative Prozesse fördern |
Es ist unsere Aufgabe, in unserem Unternehmen die Weichen für die Zukunft zu stellen und eine Kultur zu pflegen, die Offenheit für neue Technologien und Geschäftsmodelle, mutiges Agieren und eine stetige Weiterentwicklung anerkennt und fördert.

Der Wandel der Unternehmenskultur, getrieben durch die Erkenntnisse von digitalen Technologieentwicklungen, stellt damit die Basis für eine erfolgreiche Digitalisierung und damit für den nachhaltigen Unternehmenserfolg dar.
Beispiele erfolgreicher Digitalisierung in der Branche
Die Digitalisierung ist ein entscheidender Faktor für den Erfolg von Unternehmen in der Industrie. Um zu beleuchten, wie Maschinenbauunternehmen durch erfolgreiche Digitalisierung zukunftsfähig bleiben, stellen wir herausragende Beispiele der Digitalisierung vor. Diese Branchenbeispiele bieten wertvolle Einblicke in die Praxis und zeigen auf, welche Schritte zu nachhaltigem Erfolg führen:
- Automatisierte Produktionssysteme
- Digitale Vernetzung der Lieferkette
- Implementierung von IoT-Technologien
- Entwicklung Cloud-basierter Kundenportale
Ein markantes Beispiel für die erfolgreiche Digitalisierung ist das deutsche Unternehmen Siemens im Bereich der Antriebstechnologien. Siemens hat seine Produktionsprozesse durch den Einsatz von IoT und die Einführung eines digitalen Zwillings optimiert, was zu einer effizienteren Fertigung und kürzeren Entwicklungszyklen geführt hat.
Indem traditionelle Geschäftsprozesse mit modernen digitalen Technologien ergänzt werden, konnte eine gesteigerte Effizienz und eine bessere Kundenanpassung erreicht werden.
Ein weiteres Beispiel ist BOSCH Rexroth, welches durch Vernetzung seiner Geräte und maschinelles Lernen die Instandhaltung revolutioniert und vorbeugende Wartung optimiert hat.
Die folgende Tabelle gibt einen Überblick über die Transformationen und die damit einhergehenden Ergebnisse:
Unternehmen | Digitalisierungsmaßnahme | Ergebnis |
---|---|---|
Siemens | Einsatz eines digitalen Zwillings | Reduzierung der Time-to-Market und Effizienzsteigerung |
BOSCH Rexroth | Vernetzung und maschinelles Lernen | Optimierung der vorbeugenden Wartung |
KUKA Roboter GmbH | Entwicklung intelligenter Roboter mittels KI | Automatisierung komplexer Fertigungsverfahren |
Festo | Digitalisierte Lieferketten | Verbesserung der Logistik und Bestandsreduzierung |
Diese Unternehmen zeigen, dass die Integration von digitalen Technologien nicht nur zu einer steigenden Prozesseffizienz führen kann, sondern auch die Entwicklung neuer Geschäftsmodelle und Services ermöglicht. Die vorgestellten Beispiele der Digitalisierung machen deutlich, dass eine frühzeitige Adaption digitaler Innovationen ein entscheidender Wettbewerbsvorteil für Maschinenbauunternehmen in der dynamischen Industrielandschaft von heute ist.
Nachhaltige Wettbewerbsfähigkeit durch digitale Innovationen
Wir blicken auf eine Industrielandschaft, in der die nachhaltige Wettbewerbsfähigkeit von Unternehmen, insbesondere im Maschinenbau, zunehmend von ihrer Fähigkeit abhängt, digitale Innovationen zu integrieren und zu nutzen. Der in diesem Artikel dargelegte Wandel zeigt deutlich, dass die Zukunft der Industrie eng mit technologischen Entwicklungen verknüpft ist, die zu effizienteren Produktionsprozessen und neuen Geschäftsmodellen führen.
Die Anpassungsfähigkeit und der innovative Einsatz von Industrie 4.0-Technologien in der Praxis haben sich als Erfolgsfaktoren herausgestellt, die Maschinenbauunternehmen nicht nur in die Lage versetzen, aktuelle Herausforderungen zu meistern, sondern auch, vorausschauend am Markt zu agieren. Es ist diese proaktive Haltung gegenüber Innovationen, die den Grundstein für langfristigen Erfolg legt und die Branche in eine nachhaltige Zukunft führt.
Wir sehen uns vor der Aufgabe, diese Entwicklungen fortzuführen und gleichzeitig die nachhaltige Wettbewerbsfähigkeit der Unternehmen zu stärken. Dies erfordert kontinuierliche Investitionen in die Weiterbildung von Fachkräften, Sicherheitssysteme und in die Forschung neuer Technologien. Unser gemeinsames Ziel muss es sein, auf dem Fundament der digitalen Innovationen aufzubauen und den Maschinenbau als treibende Kraft hinter der Zukunft der Industrie zu positionieren.
Antworten auf häufig gestellte Fragen zur Digitalisierung im Maschinenbau
Unter Digitalisierung im Maschinenbau verstehen wir die Integration digitaler Technologien in alle Bereiche des Maschinenbaus. Dies umfasst die Automatisierung von Prozessen, die Nutzung von Daten zur Optimierung der Produktion, die Entwicklung neuer Geschäftsmodelle und die Implementierung von Industrie 4.0-Konzepten, um die Effizienz und Innovationskraft der Unternehmen zu steigern.
Unternehmen im Maschinenbau können durch Industrie 4.0 ihre Produktionsprozesse optimieren, ihre Effizienz steigern, Kosten reduzieren und neue innovative Geschäftsmodelle sowie digitale Services entwickeln. Die Vernetzung von Maschinen ermöglicht zudem eine flexiblere und effizientere Fertigung, die schnell auf Marktanforderungen reagieren kann.
Zu den Herausforderungen zählen der Bedarf an Fachkräften mit digitalen Kompetenzen, die Notwendigkeit von Investitionen in neue Technologien, der Schutz vor Cyber-Bedrohungen und die Bewältigung von Widerständen innerhalb der Unternehmen gegenüber dem Wandel. Zudem erfordert die digitale Transformation die kontinuierliche Anpassung von Geschäftsmodellen an die dynamische Technologie-Landschaft.
Wesentliche technologische Treiber sind künstliche Intelligenz (KI), Machine Learning, Big Data Analytics, Automatisierungstechniken, das Internet der Dinge (IoT) und Cloud-Plattformen. Diese Technologien ermöglichen es, Produktionsprozesse intelligenter und effizienter zu gestalten sowie neue Dienstleistungen anzubieten.
Digitale Schnittstellen und integrierte Systeme ermöglichen eine verbesserte Koordination und Kommunikation zwischen verschiedenen Bereichen der Fertigung. Dadurch lassen sich Prozesse effizienter gestalten, Fehlerquellen minimieren und die Produktion flexibel auf die Nachfrage anpassen. Das Konzept der Smart Factory wird somit zur Realität.
Das Engineering im Maschinenbau erfährt durch digitale Technologien wie digitales Design, Simulation und Engineering-Software eine signifikante Transformation. Die Fähigkeit, komplexe Daten zu analysieren und in Echtzeit auf sie zuzugreifen, ermöglicht eine effizientere Planung, Entwicklung und Herstellung von Maschinen und Anlagen.
Mit der zunehmenden Vernetzung von Maschinen und Anlagen steigt auch das Risiko von Cyber-Angriffen. Aufgrund der hohen Kosten und potenziellen Ausfallzeiten, die mit Sicherheitsverletzungen verbunden sind, ist es entscheidend, dass Unternehmen im Maschinenbau effektive Sicherheitsstrategien implementieren, um den Schutz sensibler Daten und Systeme zu gewährleisten.
Der kulturelle Wandel hin zu einer digitalen Zukunft beinhaltet das Schaffen einer offenen, innovativen und anpassungsfähigen Unternehmenskultur. Strategien zur Förderung dieser Kultur beinhalten die Weiterbildung von Mitarbeitern, die Unterstützung lebenslangen Lernens und die Ermutigung zur Übernahme von Eigeninitiative und zum experimentellen Denken im Hinblick auf neue Technologien und Arbeitsweisen.
Unternehmen im Maschinenbau, die erfolgreich digitale Transformationen durchgeführt haben, zeigen häufig eine Reihe von Gemeinsamkeiten. Dazu gehören die Einführung von Predictive Maintenance, der Einsatz von KI für die Qualitätskontrolle, die Digitalisierung des Kunden-Supports und die Verwendung von IoT-Geräten zur Echtzeit-Überwachung und -Analyse von Maschinenleistung. Namen konkreter Unternehmen werden in entsprechenden Fachpublikationen und Fallstudien thematisiert.
Digitale Innovationen ermöglichen es Maschinenbauunternehmen, Prozesse zu optimieren, Kosten zu senken, die Produktionsqualität zu verbessern und den Kundenservice zu erweitern. Diese Aspekte tragen entscheidend dazu bei, in einem sich schnell verändernden Marktumfeld wettbewerbsfähig zu bleiben und langfristig erfolgreich zu agieren.